Ils pensent le futur des voiliers
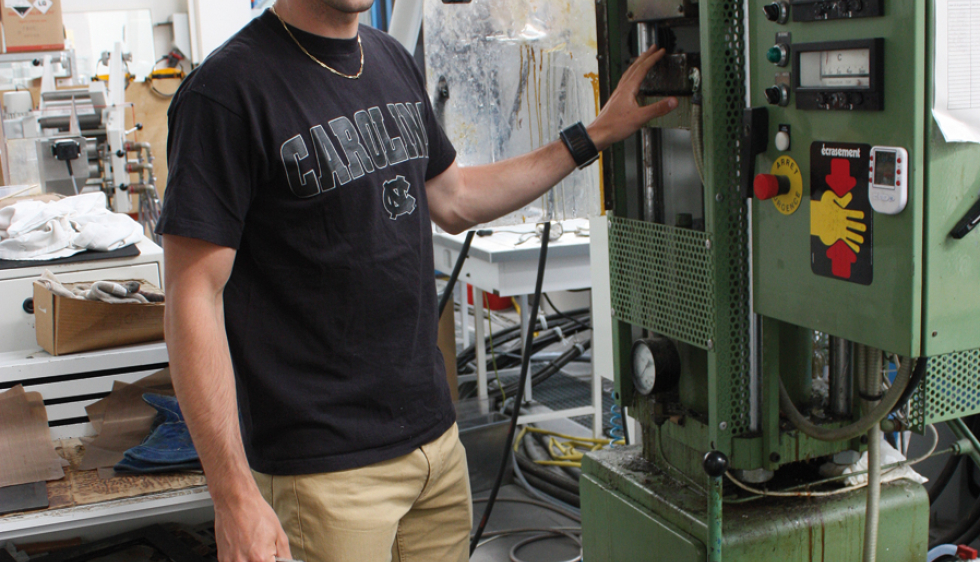
Universitaires et industriels sont réunis dans un projet collaboratif pour créer un bateau de plaisance durable.
Il devrait prendre la mer d’ici à quatre ans. Le voilier du futur, tel que l’imaginent l’association Innovations bleues et tous les partenaires du projet du même nom, prendra la forme d’un catamaran, long de 17 m. Et surtout, il sera “durable”. « L’objectif est de créer un bateau de plaisance ayant le minimum d’impact sur l’environnement, tant pendant sa navigation, que lors de sa fin de vie, explique la navigatrice Catherine Chabaud, présidente de l’association Innovations bleues. Il devra permettre de sensibiliser les plaisanciers à la préservation des océans et aussi de montrer aux industriels qu’il est possible de concevoir un tel bateau. »
L’énergie montre la route
Financé, en partie, par les Investissements d’avenir grâce à un Appel à manifestations d’intérêt lancé par l’Ademe, le projet labellisé par le Pôle Mer Bretagne Atlantique réunit des universitaires, des industriels et un cabinet d’études autour des différents postes, afin de construire un prototype exemplaire.
Côté énergie tout d’abord. Le navire devra être autonome, c’est-à-dire n’utiliser, en relais de la voile, que des ressources renouvelables : éolien, solaire et un hydrogénérateur développé par l’une des entreprises partenaires du projet, autant de sources qu’il faut savoir utiliser à bon escient. C’est tout l’enjeu des travaux de Mathilde Tréhin, en thèse au laboratoire Lab-Sticc(1) à l’université de Bretagne Sud à Lorient. Elle conçoit un logiciel capable de prendre en compte les différents consommateurs (liaison satellite, lumière, climatisation...) et les producteurs, pour les gérer au mieux. « L’idée c’est de lisser les pics de consommation. Donc d’éteindre par moment certains consommateurs, en fonction des besoins du bateau et des préférences du navigant. » Mais surtout, le système devrait pouvoir choisir la meilleure route à suivre pour optimiser la production et le stockage, en fonction des courants, des vents et de l’ensoleillement. Tout cela fonctionne grâce à des capteurs en réseaux, inspirés de ce qui existe en domotique. « Nous aimerions obtenir un système capable de s’adapter à l’environnement, qui puisse apprendre des choix successifs du marin à bord », poursuit Johann Laurent, l’un des encadrants de Mathilde Tréhin.
Repenser notre façon de faire
Pour la construction, les Lorientais travaillent également sur des matériaux recyclables et en partie biosourcés pour composer la cabine et le pont du bateau. « Aujourd’hui, les bateaux sont fabriqués en composites thermodurcissables, explique David Vaillant, jeune chercheur du laboratoire LimatB(2), des matériaux absolument non recyclables. » Ils ne peuvent pas être remodelés, ils sont broyés et éventuellement brûlés. « Nous avons opté pour du thermoplastique. Comme les composites thermodurcissables, il est composé de fibres recouvertes d’une résine plastique. Mais nous travaillons avec des fibres de lin, plutôt que des fibres de verre ou de carbone. Elles ont de grandes performances techniques et n’ont besoin que des photons du soleil pour pousser. » En fin de vie, les thermoplastiques peuvent être remodelés ou recyclés. Ils sont, par contre, plus complexes à obtenir, car une fois la fusion du polymère obtenue, c’est la vitesse du refroidissement qui va conditionner les futures qualités mécaniques du matériau. Il faut que cette étape soit bien contrôlée, et cela nécessite des équipements capables d’atteindre des températures élevées. « Il faut repenser notre façon de faire, ajoute Christophe Baley, son responsable, déjà présent lors du programme précurseur Navecomat(3). Il faut imaginer les moules, les processus de transfert de technologies. Nous travaillons pour cela avec Multiplast, un industriel vannetais. »
Éviter les inconnues
À l’heure actuelle, les chercheurs savent créer, en laboratoire, des plaques d’environ un demi-mètre carré. Tout le défi du projet est de passer à grande échelle. La thèse de David Vaillant va également permettre d’approfondir les connaissances sur les qualités mécaniques du matériau : sa réponse aux sollicitations, aux UV, à l’eau de mer, sa réparabilité, son vieillissement. Ce dernier point sera étudié avec l’Ifremer de Brest.
« Aujourd’hui les composites classiques tiennent quarante ans. Nous allons vers la même durée de vie. Ensuite le thermoplastique peut être broyé pour obtenir un nouveau composite à fibres courtes, pour faire des cagettes, des chaises... » Les chercheurs parviennent ainsi à le réutiliser sept fois en laboratoire. « Il faut également penser à l’assemblage des pièces, poursuit Christophe Baley, question que l’on ne se pose pas sur un bateau classique car il n’y a pas d’objectif de démontage ! » Au LimatB, les chercheurs travaillent aussi sur des résines biosourcées. Mais elles ne seront pas mises en œuvre dans le voilier du futur. « Les délais sont trop courts, on ne peut pas prendre le risque de tout faire tomber à l’eau en intégrant trop d’inconnues ! » De même la coque ne sera pas en biocomposite, mais en aluminium, un métal recyclable.
Qu’importe, ce premier pas sera déjà une grande avancée dans le monde de la voile, peu investi dans ce genre de recherche. « Dans la course au large, on peut innover car il y a des sponsors, donc des financements. » L’entreprise Kaïros du navigateur Laurent Jourdain, qui travaille également avec le LimatB sur les biocomposites en est un exemple. « Dans la plaisance c’est beaucoup plus compliqué. D’où l’intérêt d’un projet collaboratif. » L’ensemble de ces innovations, et d’autres, comme la peinture antifooling biodégradable, par exemple, ou des systèmes de sécurité innovants, sont directement intégrés dans une analyse de cycle de vie, réalisée par le bureau d’études nantais Evea, grâce à un logiciel, Convenav, développé il y a quelques années en collaboration avec Lorient, toujours. Pour assurer un avenir propre au bateau du futur.
(1)Laboratoire des sciences et techniques de l’information, de la communication et de la connaissance UMR CNRS 6285.
(2)Laboratoire d’ingénierie des matériaux de Bretagne EA 4250.
(3)Lire Sciences Ouest n° 256 - juillet-août 2008.
www.innovations-bleues.org
Gwenaël Le Maguer
gwenael.le-maguer [at] univ-ubs.fr (gwenael[dot]le-maguer[at]univ-ubs[dot]fr)
Johann Laurent
johann.laurent [at] univ-ubs.fr (johann[dot]laurent[at]univ-ubs[dot]fr)
Christophe Baley
Christophe.baley [at] univ-ubs.fr (Christophe[dot]baley[at]univ-ubs[dot]fr)
David Vaillant
David.vaillant [at] univ-ubs.fr (David[dot]vaillant[at]univ-ubs[dot]fr)
Mathilde Tréhin
Mathilde.trehin [at] univ-ubs.fr (Mathilde[dot]trehin[at]univ-ubs[dot]fr)
TOUT LE DOSSIER
du magazine Sciences Ouest